Knowledge Base Page - Solution-Dyed Fabrics
Aug 12, 2019
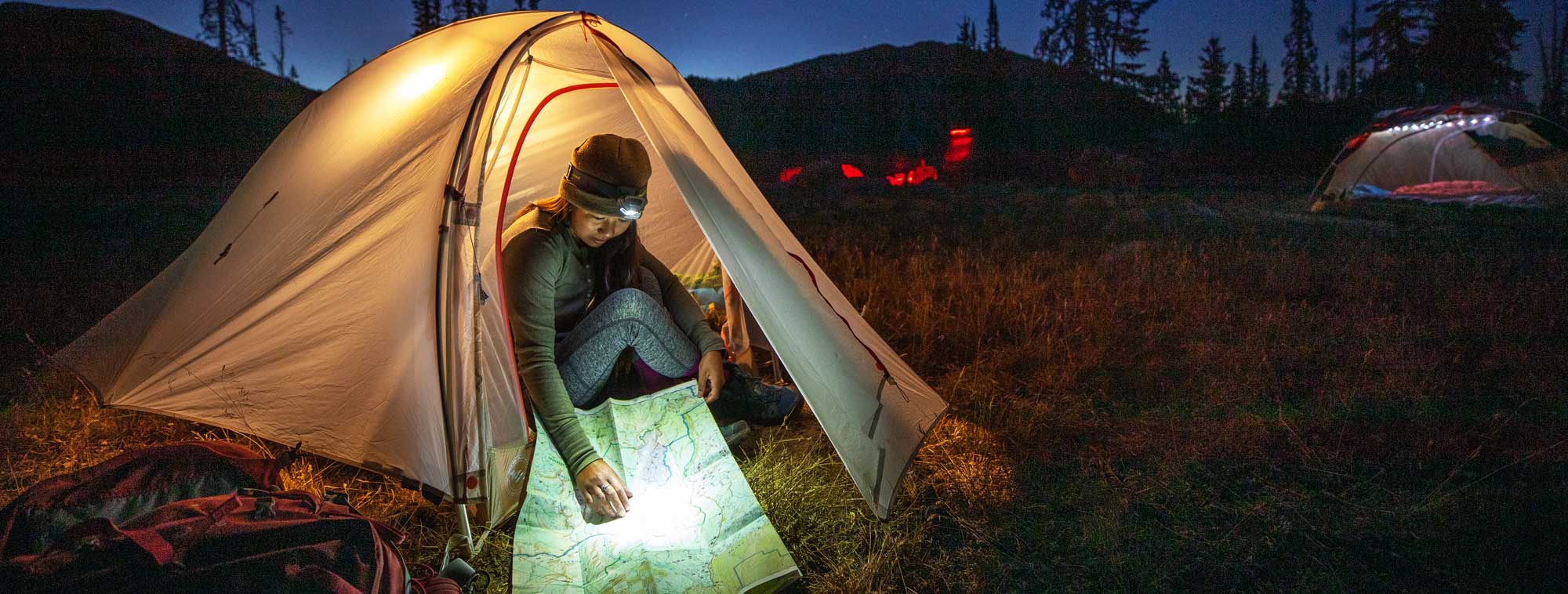
The Solution-Dye Process
In simple terms, solution-dyeing is a technique that reduces the use of water and chemicals when dyeing fabrics compared to traditional wet processes. The solution-dye process involves mixing the colour pigments in with raw or recycled polyester, before they are made into filaments. By dyeing the fibres without water, there is a reduction in chemical waste, energy usage and bi-products such as CO2.
Solution dying is a technique used to colour synthetic textiles such as acrylic, nylon and polyester. The solution dye process differs from traditional fibre or piece dyeing since it involves one less process step. In the solution dye process, pigments are added to the liquid polymer solution before synthetic fibres are extruded. Compared to traditional fibre dyeing – where colour is applied in a second process step; after fibres have been extruded. The solution process saves approximately 80% water, 20-30% dyestuff, 80% other chemical agents and it also requires less energy.
A Comparison Between the Two Techniques:
Solution Dye Process - Fibres and filaments are coloured before knitting
Traditional Dye Process - Fibres and filaments are knitted first and then coloured, offering a larger selection of colours
*
Solution Dye Process - Shorter lead time due to avoiding the dying process: buyers know precisely the colours before they order
Traditional Dye Process - Longer lead time due to the need to verify the colours first via lab-dips
*
Solution Dye Process - Excellent colour fastness, resistant to multiple washing, great for bright colours, resistant to UV fade
Traditional Dye Process - Colour fastness depending on used material and other factors, but generally worse than the dope dye
*
Solution Dye Process - No water is used during the dope dyeing process, chemicals and carbon is reduced, lower energy use
Traditional Dye Process - Production is not environmentally friendly, with high water, CO2, chemical and power consumption
Brand Involvement:
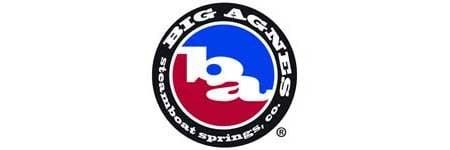
Big Agnes is the first to introduce solution-dyed fabrics to the camping equipment category. Tents made with solution-dyed fabric drastically reduce water and energy consumption during manufacturing. Solution dyeing of our tent fabrics reduces energy consumption by 80% and water use by 50% compared to traditional fabric dying methods. The result is better for the environment and the fabric improves the quality of our tents. Solution-dyed fly and inner tent fabric is used in 9 different 2021 tent models.
What does Solution-Dyed mean? Solution-dyed fabric is produced from yarn made from pre-coloured chips of nylon or polyester verses fabric made from uncoloured yarn which is then colored. Imagine a carrot vs. a radish. One is colored throughout and one is only coloured on the outside.
- 80% reduction in energy required - Carbon savings but data TBD
- 50% reduction in water required - Nearly 5 gallons of water saved on some tent models.
- Estimated 45,000 to 80,000 gallons saved for 2021 season tent production alone.
-Solution-dyed yarn is highly resistant to UV fade and shade changes.
- Solution-dyed yarns and fabrics woven from them are uniform in color and typically don’t vary from lot to lot as they start with pre-colored chips
Shorter lead times for fabric production as the lab dip and approval process is removed and less fabric is wasted due to incorrect dye process.
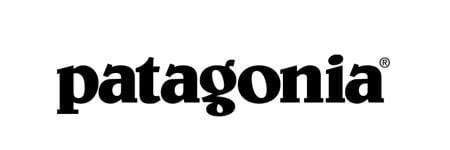
Conventional batch-dyeing processes (using synthetic dyes) require a tremendous amount of water and energy, resulting in waste and carbon emissions. Patagonia switched a selection of our products to solution dyeing, an approach that can result in up to 90% reduction in water use and 96% CO₂e savings overall compared to batch-dyeing, with considerably fewer chemicals released from the overall process.
Solution dyeing diverts from traditional wet processing. Pigment is added to the molten plastic before making the fiber. Since the yarn is created in a specific color (versus first being produced and then dyed), the color is confined within the yarn. Imagine little pigment molecules becoming trapped inside the plastic after it cools to a solid form. The color becomes intrinsic to the yarn through solution dyeing, so the process often yields stronger fibers than batch dyeing, which weakens and damages the fiber’s integrity.
One of our main goals in incorporating solution dyeing is to reduce the amount of water used in the textile-coloring process. Other water-free dyeing techniques are being developed, and companies (including Patagonia) are building a better understanding of the advantages and disadvantages of this process. We’ve also recently learned that solution dyeing could be a potential answer to reducing microfiber shedding—making it a win (low carbon)/win (low water)/win (reduced shedding) for the environment. We’re working with suppliers and researchers to gather more data about this.
One of the lone downsides of solution dyeing is that it can only be applied to synthetic fibers. But strides are being made to change how organic fibers can be dyed in a more sustainable way—even though research and experimentation are still at an early stage. Cotton, for example, can be grown in different colors to achieve new pigmentation, but this method brings a host of other challenges at the agricultural level.
We are continuing to look for efficient dyeing technologies and techniques, and we’re striving to adopt new options as they become available. Ultimately, solution dyeing will be part of a portfolio of technologies that reduces our impact on the planet.
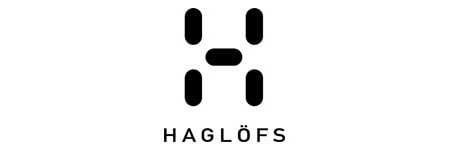
Although synthetic fibers have only been around for about 60 years, they are dyed using a process that’s been around for centuries. This process, where the fabrics are dipped in dye baths, coloring the outside of the fibers, was pioneered long before synthetic fabrics were invented and is more suitable for natural fibers such as cotton and wool. The process uses lots of energy and creates large amounts of wastewater.
Solution-dyed fabrics on the other hand, have the color added to the material right at the very start - when the fibers are being created and spun. This process eliminates the need for baths of dye - reducing water consumption, energy use and the risk of dyed water contaminating the local environment.
You’ll find solution dyed fabrics in many of our footwear styles along with a growing number of Gore-Tex jackets.
In this post we look at solution dyed fabrics and explain why they are more environmentally friendly.